Services
1. Process Safety management (PSM) through project life cycle Corporate HSE Management
Process safety management is a regulation, promulgated by the U.S. Occupational Safety and Health Administration (OSHA). A process is any activity or combination of activities including any use, storage, manufacturing, handling or the on-site movement of highly hazardous chemicals (HHCs) as defined by OSHA and the Environmental Protection Agency. Process Safety Management is focused on preventing releases of any hazardous substance. It refers to a set of inter-related approaches to manage hazards associated with the process industries and is intended to reduce the frequency and severity of incidents resulting from releases of hazardous substances incompliance with the standards of organizational and operational procedures, design guidance, audit programs, and a host of other methods. The process safety management program is divided into 14 elements
1. Process Hazard Analysis
2. Operating Procedures
3. Training
4. Contractors
5. Mechanical Integrity
6. Hot Work
7. Management of Change
8. Incident Investigation
9. Compliance Audits
10. Trade Secrets
11. Employee Participation
12. Pre-startup Safety Review
13. Emergency Planning and Response
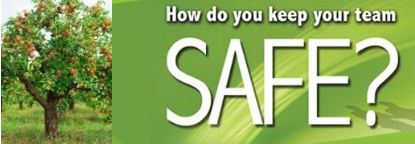
All of those elements mentioned above are interlinked and interdependent. There is a tremendous interdependency of the various elements of PSM. All elements are related and are necessary to make up the entire PSM picture. Every element either contributes information to other elements for the completion or utilizes information from other elements in order to be completed.
2. Authoring of HSE Safety Case/ Design Safety Case
HSE Safety Case/Design Safety Case is a structured argument, supported by evidence, intended to justify that a system is acceptably safe for a specific application in a specific operating environment. Safety cases are often required as part of a regulatory process, a certificate of safety being granted only when the regulator is satisfied by the argument presented in a safety case. The review of safety cases is an important activity in the safety engineering process, performed throughout development, operation and maintenance n which the safety case argument and evidence are scrutinized and challenged.
A safety case aims to show that specific safety claims are substantiated and, in the UK, that risks are kept 'As Low As Reasonably Practicable' (ALARP). Safety cases are typically documented in both textual and graphical notations, Following are the key step of Safety Case Lifecycle.
1. Propose & Plan
2. Develop
3. Review
4. Submit
5. Implement
6. Improve
7. Revise
8. Audit
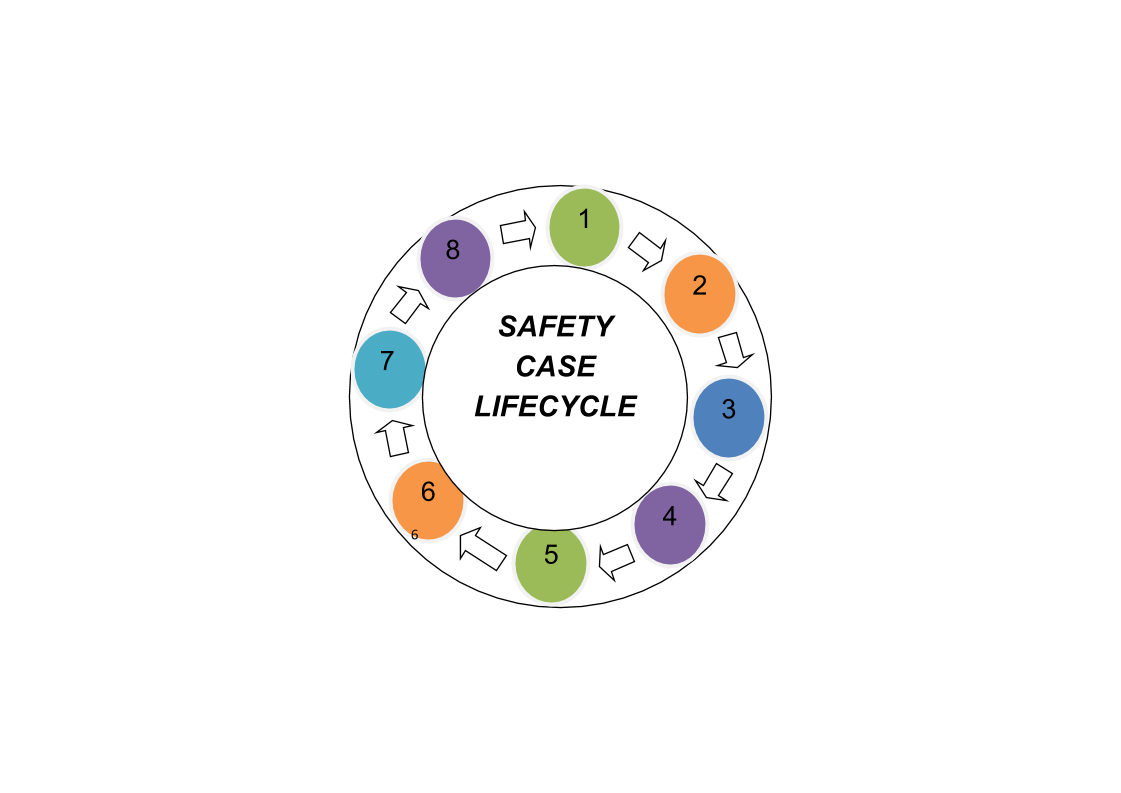
3. Pre Start-up Safety Reviews (PSSR)
The PSSR is a safety review conducted prior to startup (commissioning) of a new or modified processing/manufacturing plant or facility to ensure that installations meet the original design or operating intent, to catch and re-assess any potential hazard due to changes during the detailed engineering and construction phase of a project. In other words, it ensures the “Ready for Start-up” status of process facility/units.
A Pre Startup Safety Review covers not only equipment, but also procedures and training. Pre Startup Safety Review procedure/guideline is normally prepared as part of Pre-commissioning/ commissioning documentation.
The Main Propose of the PSSR is
1. To ensure that installation meets the original design and operating intent of process plant/facility
2. To ensure safety, operating, maintenance and emergency procedures are in place and adequate
3. To ensure appropriate safety reviews during engineering phase (different Safety Studies) have been carried out and all action items have been completed
4. To ensure any site modifications during construction phase have been properly controlled and noted
5. To ensure training of each employee involved in the operating process is completed
6. In addition, the pre startup safety review plays an important role in large projects as it may give plant operators the authority to refuse or accept responsibility for a plant or equipment that they judge to be unsafe through the PSSR.
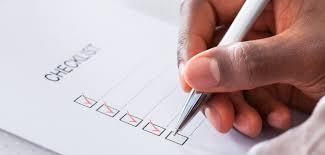
4. Job Safety Analysis (JSA)
A job hazard analysis (JSA) is a technique that focuses on job tasks as a way to identify hazards before they occur. It focuses on the relationship between the worker, the task, the tools, and the work environment.
There are four basic steps involved under JSA:-
- Selecting the job to be analyzed
- Breaking the job down into a sequence of steps
- Identifying potential hazards
- Determining preventive measures to overcome these hazards
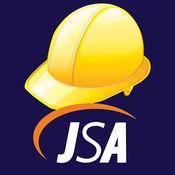
An advantage of this method is that more people are involved in a wider base of experience and promoting a more ready acceptance of the resulting work procedure.
Initial benefits from developing a JSA will become clear in the preparation stage. The analysis process may identify previously undetected hazards and increase the job knowledge of those participating. Safety and health awareness is raised, communication between workers and supervisors is improved, and acceptance of safe work procedures is promoted.
5. Critical Task Analysis (CTA)
Critical Task Analysis is a methodological process used to determine what if special controls or attention should be put into place when doing non-routine work
It is an essential skill for occupational health and safety officers, supervisors, and managers in any organization. The ability to identify critical tasks and assess them for hazards and loss control opportunities will assist greatly in making critical tasks safer to achieve, and reduce the loss and accident rate for any organization.
A simple step wise process of Critical Task Analysis is given below
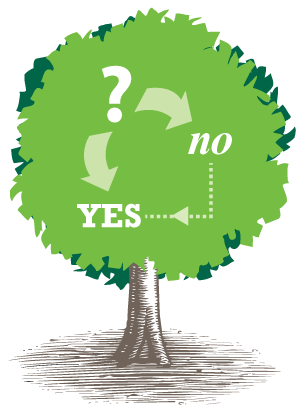
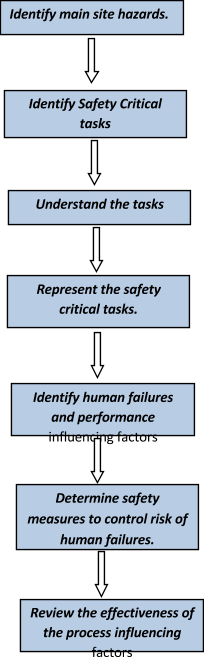
6.Corporate HSE Management
The Corporate HSE Management System defines the principles by which an organization conducts its operations be it at single facility or multiple locations worldwide with regards to health, safety, and the environment. The organization’s top management communicates the HSE philosophy to all employees, customers, contractors, and third parties associated with their business, and each entity within the organization must provide positive evidence of conformance to the system. The HSE Management System model comprises of the following broad elements:
- Leadership & management’s commitment,
- Employee participation
- Process safety information
- Risk analysis and management,
- Reliability of critical devices and control of defeat
- Permits and authorization to work
- Operation and maintenance philosophy
- Inspections
- Audits and system for continual improvement
- Accident prevention analysis
- Investigation and reporting,
- Compliance to applicable regulations
- Standards and guidelines
- Emergency planning and response etc.
7.HSEIA
The Health, Safety and Environmental Impact Assessment (HSEIA) is a systematic process of identifying the impact of existing, new or substantially altered projects on health, safety and the environment.
Nowadays, the impact of process industry / manufacturer operations on the health and safety of their staff and that of the communities in which they are located, as well as the surrounding environment, is coming under scrutiny from various regulatory authorities. It is therefore important that an organization is able to identify and mitigate any issues that might have an adverse effect on these HSE areas.
The main objectives of a Health, Safety & Environmental Impact Assessment (HSEIA) Report are to demonstrate:
- Compliance with HSE legislation and standards;
- All HSE hazards, including major accident hazards and occupational health hazards, have been systematically identified, assessed and mitigated;
- The environmental impacts have been identified, assessed and mitigated.
The HSE impacts and risks of a project are initially identified through a combination of workshops and scoping studies, and then compiled into a Hazards and Effects Register.
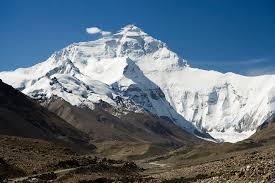
8. COMAH
Control of Major Accident Hazards Reports apply to operators with specified quantities of defined dangerous substances on their site, and require the operators to take all measures necessary to prevent major accidents. COMAH safety reports demonstrate that measures are in place to prevent major accidents and limit the consequences if they occur. In other words, they should describe not only what, but why these particular measures together are thought to prevent and limit major accidents. COMAH applies mainly to the chemical industry, but also to some storage activities, explosives and nuclear sites, and other industries where the threshold quantities of dangerous substances identified in the Regulations are kept or used.
The COMAH purpose is to deliver a safety regime aiming to:
- Ensure that those responsible for creating risks meet their responsibilities to manage them;
- Ensure that suitable emergency arrangements are in place and work;
- Assure people living or working near a ‘major hazard’ establishment that the operator takes their safety and that of the surrounding environment into account;
- Help industry to conduct its activities safely and recognize that individual failures undermine the sector as a whole;
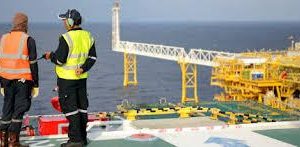
9. Safety Audits
Safety Audit is an important tool for assessing the strength and weaknesses of Safety Management System of the organization. Safety Audit should therefore be an integral part of a Company’s control system. The technique of safety audit subjects each area of company’s activities to a critical systematic examination with the object of minimizing losses.
The audit, as in the field of accountancy, aims to disclose the strengths and weaknesses of the organization and the main areas of vulnerability or risk and is carried out by appropriately qualified team through structured audit techniques. The safety audit includes all major components of the Occupational Safety & Health System.
The following are the goals of the Safety Audits
- To provide an opportunity to assess its own Occupational Safety & Health system and identify areas of improvement;
- To determine the conformity of the implemented systems with specific requirements and identify areas of improvement;
- To meet regulatory requirements
The safety audit has the following objectives
- To carry out a systematic, critical appraisal of all potential hazards (mainly with process) involving personnel, plant, services and operation methods; and
- To ensure that OS & H system fully satisfy the legal requirements and those of the company’s written safety policies, objectives and progress.
There are 4 Stages involved in a Safety Audit
- Pre audit activities: During this phase Kick of Meeting, appropriate questionnaires and observation worksheets are customized based on the valuable inputs provided by the Company.
- Onsite Activities: During this phase visits are carried out to the various locations of the facilities. During these site visits, detailed site inspections are conducted, discussions held with personnel at the site level including management, supervisors, workmen and casual labour deployed in order to check and verify ground realities. In addition, the several documents and evidence were collected and examined and a “spot check” on a random basis done and points of concern identified
- Closure of Meeting: A meeting with the plant personnel will be held at the site to inform them about the observations in brief
- Post visit Activities : This phase-included compilation of information, observations – compliance, deviations, and recommendations and compilation of the Draft Safety Audit Report and Final Reports.
- Specialized safety training courses (Fires, HAZOP Leader, HAZOP Scribe, Consequence Modeling etc.)
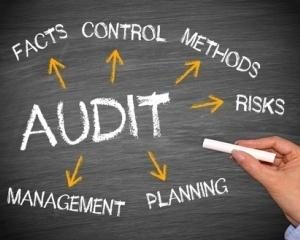
Our in-house experts have cumulative experience of over 100 years in rendering HSE studies and also provide training to clients teams in fire fighting techniques, PSM, HAZOP leadership, Hazop scribe, quantitative risk assessment, Permit to work systems, emergency planning and response, consequence modelling, accident analysis, investigation and reporting, Mock Drills, DMP, ERP, Chemical Hazards, GIS based Emergency Planning and Response Systems, Environment Protection etc.
Following are the companies for which the training are provided.
- Jubilant Life Sciences Ltd.
- UFLEX Industries
- Indraprastha Gas Limited
- National Thermal Power Corporation
- Frito Lays India Pvt. Ltd.
- National informatics Center
- Haryana Institute of Public Administration (HIPA)
- Gujarat State Petronet Ltd.
- District Crisis Group (DCG), MOEF &CC
- National Workshop on Transportation of Hazardous chemicals
- NDMA
- Ramco Industries Ltd
- UNIDO (UN agency) and Indian Petrochemicals Corporation Ltd.
- US AID and Indian Institute of Technology, Delhi
- Indian Institute of Technology, Delhi
- HRD Foundation and Ministry of Environment and Forests, Government of India
- Ministry of Environment and Forests, Government of India and Environment Canada and UNITAR (United Nations Institute of Training and Research)
- Indian Chemicals Manufactures Association
- Hyderabad Bulk Drug Manufacturers Association
10.F&G Mapping and Optimization
Fire & Gas Mapping and Optimization systems should play a crucial role in Loss Prevention on many sites. Formal Safety Assessments such as Quantified Risk Assessments (QRA) often assume that Fire and Gas Detection Systems will reduce risks, yet their design is often a matter of “black art”; it is often difficult to quantify the parameters involved and there is little guidance to define required performance or to relate achieved performance to safety requirements. Modern fire and gas detection designs tend towards hazard based approach featuring recognized and quantified hazards,
A Fire and Gas Optimization Study shall be performed based on Plot plan, PFD’s, P&ID’s and Stream Data for the facilities. The following steps are followed during the study:-
- Identifying leak locations & based on the methods for evaluating consequences, consider leaks from a specific diameter opening (complete breakage, which is the worst-case scenario for pipes.
- Establishing initial gas detector locations
- Determination of threshold release rate by dispersion simulations
- Confirming validity of threshold release rate
- Evaluating appropriateness of gas detector locations
- Confirmation of leak detect ability with multiple gas detectors
- Optimizing placement of gas detectors using tools for calculating atmospheric dispersion. Suitable detection of gas leaks using gas detectors is indispensable for absolutely assuring no damage to the general off-site population with measures for emergency plans.
- Reviewing the provisions of new Fire & Gas detection systems and its integration with existing fire & gas detection panels in Central Control Room and/or in DCS and Reassessment of gas detector locations
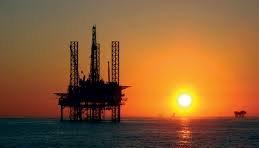
11.Chemical Compatibility Matrix and Storage Plans
Chemical Compatibility Matrix is a shorthand tool for describing the suitability of miniature fluidic and pneumatic component materials for use in contact with various chemicals. Use this matrix as a help guide to the component selection. It is also useful in safe handling of the chemicals and keeps to working environment safe. Incompatibility matrix can be used to avoid hazard scenarios that may occur during handlings certain hazardous chemicals may come in contact with each other resulting in violent reactions due to their incompatibility.
General Guidelines for Safe Storage
- Always store chemicals by recommended compatible storage group. Alphabetical storage is only used within a compatible storage group, never as a chemical storage plan.
- When determining how to store the chemical, always check the chemical label and MSDS/SDS first for the manufacturer’s recommended compatible storage.
- Keep chemicals away from ignition sources. Store flammable and combustible chemicals in an approved flammable chemicals storage cabinet.
- Avoid storing chemicals in direct sunlight or near a localized heat source.
- Store flammable and potentially explosive chemicals according to the manufacturer’s directions or according to MSDS instructions.
- Use secondary containers to physically segregate incompatible chemicals when they are stored in the same physical location.
- Label and date chemical containers when received and opened. Label working solutions or chemicals removed from their original container so that all individuals know what is in a given container.
- Maintain chemical identification labels, containers, and lids in good condition.
- Keep chemical containers closed with properly fitted caps when not in use.
- Hazardous chemicals must not be stored above shoulder height.
- Do not store stock chemical supplies in a fume hood. This interferes with proper hood airflow and can provide fuel if there is a fire within the fume hood. Flammable chemicals should not be stored in a fume hood.
- Chemicals should never be stored on the floor.
- Chemical shelving should have containment lips or trays to contain small leaks/spills. Chemical cabinets should have a leak proof door sill.
- Shelving should be strong enough to hold the weight of chemicals being stored on them. Do not overload shelves. Always secure shelving to a permanent structure. Shelves should be coated with a chemical resistant material such as chemical-resistant paint or another coating such as epoxy.
- Do not store chemicals in a domestic refrigerator or walk-in cooler. These refrigeration devices contain ignition sources such as unsealed electrical contacts. Flammable-safe refrigerators should be used whenever flammable chemicals need to be refrigerated. Additionally, walk-in coolers are not vented, creating the potential for accumulation of chemical vapors.
12.Preparation of Facility and Area Disaster Management Plans and mapping potential disaster consequences through GIS
Planning for responding to emergencies is one of the critical components of the corporate HSE management system. Although provision of safety system usually ensures prevention of accidents, if and when it occurs, has the potential to adversely impact the employees, asset and the environment. Responding to emergencies in a systematic and structured manner is therefore imminent for minimizing the loss. Disaster management plan provides the framework for dealing with emergencies. The main components includes identification of hazards, their consequences, response facilities available and a well defined team with specific roles and responsibilities to be carried out during an emergency to reduce/eliminate potential loss
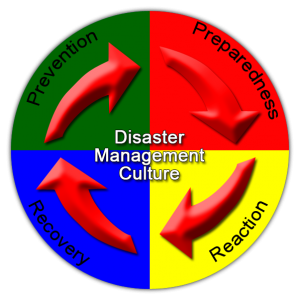